How NDT Testing Helps Detect Hidden Defects in Materials
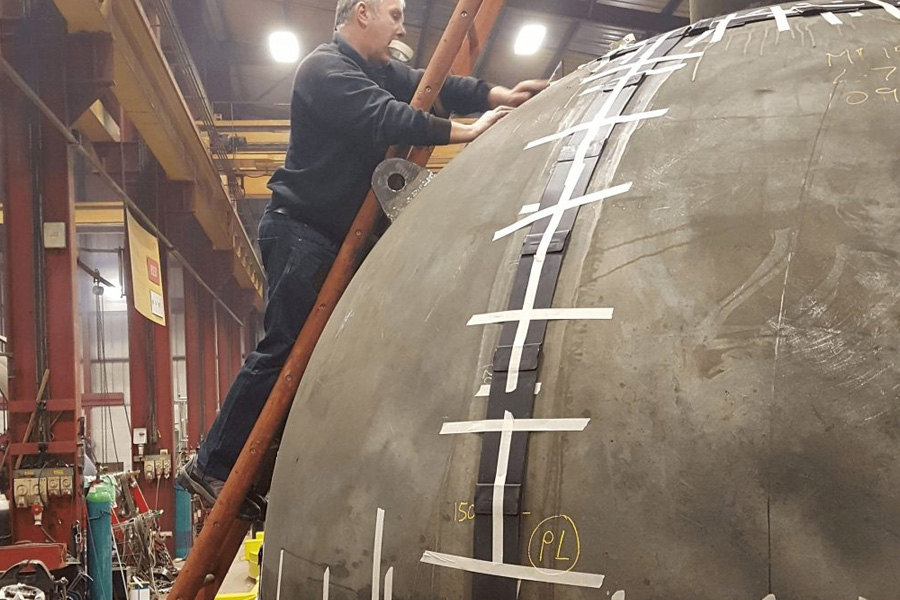
Image Source: www.formatndt.co.uk
Securing and ensuring the reliability and quality of materials used in various kinds of industries is a great role played by Non-Destructive Testing. Unlike the traditional techniques of destructive testing, NDT allows engineers and technicians to check materials and components for hidden defects without causing any damage to the materials. This article deals with how the NDT test helps in revealing hidden defects in materials by showing their importance, techniques, and areas of application.
What is NDT Testing?
NDT Testing is the term that defines the whole range of testing methods that enable to investigate the properties of a material, a component, or a structure without damaging its ability to perform. Its principal sectors are aerospace, construction, manufacturing, automotive, and oil and gas. Due to NDT tests, specialists can detect flaws before a failure or even destruction; therefore, they do not have to pay significant sums for repair or suffer critical accidents.
How Does NDT Detect Hidden Defects?
All materials made up of metal, plastic, or composite deteriorate with time. Such defects can’t be detected by the naked eye but can significantly affect both the performance and safety of the material. NDT discovers these invisible problems with the help of technology and through internal flaw visibility without damaging the material.
Some common hidden defects are as follows:
Cracks:
Tiny, internal cracks or fractures, which propagate under stress or strain that, may cause material failure
Corrosion:
Damage as a result of chemical reaction between the material and environment, causing weakening of structures.
Porosity:
Small pockets of air within the material and can cause weakening of material strength and durability.
Weld defects:
Imperfection in weld joints that can lead to weakening of a structure hence compromising the integrity of the structure.
Inclusions:
Internal foreign material that is enclosed inside the material, which also decreases the strength and ability to perform.
NDT tests allow early discovery of potential hidden defects thereby providing accident-free, durable materials in support of quality products.
Other Most Widespread NDT Methods Used To Discover Hidden Defects
Among many different types of NDT, different techniques are applied. Each one has a peculiar procedure suitable to find a given type of defect in certain material. The most universally accepted ones are:
1. Ultrasonic Testing (UT)
Ultrasonic testing is the process of locating internal flaws such as cracks and voids within materials by using ultrasonic sound waves. The returning waves are measured after their transmission into the material. Since the pattern of the discontinuities or flaws will modify the sound wave, there will be detection, and it can be further analyzed. UT is greatly applied in metal and concrete inspection.
2. Radiographic Testing (RT)
Radiographic testing uses the passage of X-rays or gamma rays into a material, whereby an image of its inside make-up is created. It is very effective in analyzing cracks and other defects developed in a material. The application of RT is mostly done in industries such as aerospace, oil and gas, and manufacturing, since parts with vital functions in those industries must be established for integrity.
3. Magnetic Particle Testing (MPT)
The magnetic particle test is the method for identifying whether there are surface and near-surface defects in ferromagnetic materials like steel. A small amount of fine iron powder is applied on the material surface after magnetizing the material. The particles will cling to the flaw in the case of a crack or defect, thus making it visible. MPT is very useful in the identification of cracks, seams, and other surface defects in metallic materials.
4. Dye Penetrant Testing (DPT)
Dye penetrant testing is one of the simplest yet effective methods to find surface-breaking defects in non-porous materials. An electrolyte or a fluorescent dye is applied to the material, which is allowed to act for a few minutes and after that, excess liquid wiped off. The material under ultraviolet light shows the crack or defects which have been absorbed by the dye. This method is suitable especially when cracks, porosity, etc., are detected in surface imperfections of metals, plastics, and ceramics.
5. Eddy Current Testing (ECT)
Eddy current testing is a technique for detecting surface and sub-surface defects in conductive materials through electromagnetic induction. This technique uses a coil that generates an alternating current and hence a magnetic field. As the coil moves over the material, any defect inside the material causes a disturbance in the magnetic field, which can be measured. ECT is very effective in detecting cracks, corrosion, and other defects in metals such as aluminium and steel.
Why NDT Testing is Important
There are several reasons for this fact:
Early Detection of Defects:
NDT tests allow to detect hidden defects much early in life and even enables possible failures to avoid those occurrences before they would really lead to costly extensive damages or accidents.
Cost-Effective:
This prevents all costs on the expenses needed for repair or replacement with additional losses that also impact downtime. Reduces all costs on unnecessary expensive over-processing to guarantee workers safety at site.
Better Quality and Safety:
NDT would ensure that materials and constituents meet the set standards of quality according to requirements of the regulatory body. In this way, it preserves the safety of goods, buildings, and mechanical equipment.
Longer Material Life:
NDT is an excellent tool for a long material life. It is based on the detection of impending ailments before they become catastrophic. It ensures one avoids potential untimely replacements.
Non-Destructive:
NDT does not have the characteristics of destructive testing since materials and parts may be in service while on inspection without causing unnecessary wastage and loss of productive time.
Applications of NDT in Various Industries
NDT testing is applied to different industries to find the quality and safety of the material. The most prominent fields where NDT is being used are:
Aerospace:
The materials in aircraft must be safe and reliable for use in the aerospace sector. NDT helps make sure that wings, fuselage, and even the engine are free from defects so flight safety is not compromised.
Construction:
NDT examines the structural materials used like the beams made of steel and concrete, and the welds so that buildings and bridges are safe for use.
Oil and Gas:
NDT determines any corrosion, cracks, or even some defects within pipelines and containers used during drilling, possibly liable to leak or even cave-in catastrophically.
Automobile:
NDT on parts like engines, chassis, and exhaust systems- in them hidden defects exist affecting either running of vehicles or even safety.
Power Generation:
From NDT, there is definite assurance that pressure vessels in nuclear power plants, turbines, as well as reactors, are entirely free from imperfections liable to result in hazardous states or system failure.
NDT testing is a very potent tool for the detection of hidden defects in materials thereby ensuring safety, reliability and quality in many industries. Through ultrasonic, radiographic, magnetic particle, dye penetrant, or eddy current testing, NDT provides a non-destructive method to identify probable defects before they become severe faults. That therefore means that failures are prevented; cost savings, and materials’ lifespan, so, NDT is critical in preserving the integrity of the critical assets, as well as protecting people and the environment.