9 Top Reasons Why Welded Joints Fail
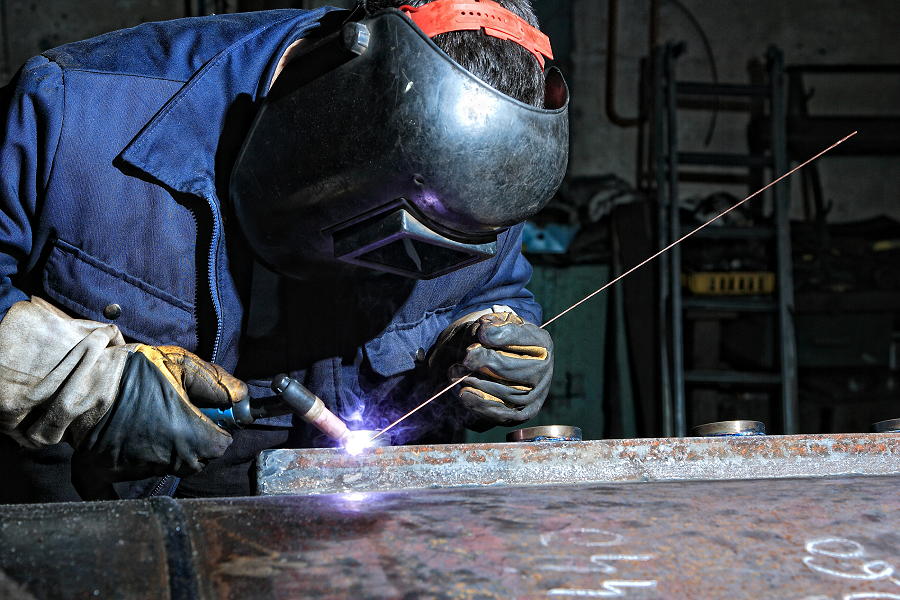
Welded joints have imperfections that can now easily be avoided. It’s important to drive down the costs of projects by using quality materials. Below are some of the most common reasons why welded joints fail and what your options are when it comes to custom steel fabrication.
1. Cracking
Cracking occurs when there’s a build-up of stress that has accumulated with the heated metal. The stress can be relieved through various methods, but cracking is something that is deemed unavoidable for most smaller projects. Using lower temperatures allows the cracking to be prevented.
2. Low heat
If the weld joints are not hot enough, then you are going to run into different problems in the future. It’s important that you are using enough heat so the weld joints won’t be considered weak. A cold object can’t be manipulated in the same manner as a hot one.
3. Oxidation
Oxides can and will prevent the forming of a quality weld. Because hot metals oxidize, you have to make sure that you get the metal to a hot temperature. Hot enough that it can prevent the oxidation by using a gas shield. You can also use a rod that contains carbon inside of it to bond with the oxygen.
4. Corrosion
Weld joints fail more often than not due to chemical degradation. If there is a weak point in the metal due to the corrosion, the entire thing might start to fall apart. The heat-affected zone has to be carefully monitored to prevent rust from forming on the material.
5. Moisture
Moisture is the primary cause of bubble pockets. Bubble pockets can be easily noticed when you are working on custom steel fabrication, so they can be easily resolved. You just have to make sure that the metal parts are dry to prevent porosity from forming as you proceed with the welding.
6. Dirt
Any kind of dirt and debris that goes onto or even into the welded joints can become a headache later on. Make sure that the area is clean as you work. Dirt and debris can cause uniformity to degrade with the weld joint during the welding process.
7. Inexperienced worker
The welder should be someone who is experienced with the procedure. An inexperienced worker is more than likely to make mistakes that can cause the welded joints to fail in the future. Having better workmanship is likely to increase the overall quality and durability of the output.
8. Incorrect logistics
The workers don’t necessarily need to know the breakdown of cost analysis as they work on the custom steel fabrication. However, they should have an idea of what they are going to work with. A training program before welding begins can help orient them with their duties.
9. Equipment defects
Using defective equipment can cause the welded joints to suffer in terms of quality. Even if you follow the design down to the centimeter, you are still going to come out with an undesirable fabrication if you are using equipment that’s not up to par.
For your custom steel fabrication needs, only tap the services of tried and tested welding companies such as KLK Welding. Contact us today and let’s discuss the project you have in mind.